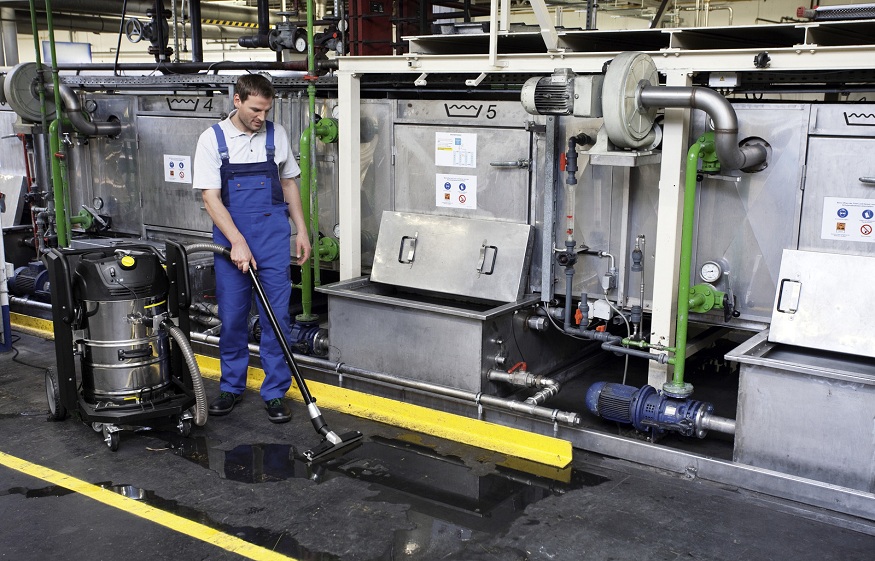
Whenever there is a problem with the amount of dust that has gathered in your facility, performing ordinary housekeeping might consume a significant amount of time. The amount of time spent cleaning up dust in an industrial setting can be significantly reduced by using a central vacuum system. Additionally, the NFPA standards are more easily met and safety is increased with this type of system. If you want to maintain your facility clean, you should consider investing in a central dust collector rather than sweeping and vacuuming on a spot-by-spot basis.
What exactly does it mean when someone refers to a “centralized vacuum system”?
When an industrial plant has huge work spaces and production departments which are located in different parts of the facility, it can be challenging to maintain optimal and consistent cleaning which satisfies high hygiene standards. Even if they are effective and simple to operate, conventional industrial vacuum cleaners are unable to address the issue of cleaning in multiple locations at the same time.
The centralized vacuum systems that are now on the market are the best solution. It will enable us all to extract as well as transport material through one location to another through a system of pipes, as well as allow us to accumulate it and discharge it at a particular point. It is composed of numerous different elements.
HOW THE CAPACITY OF THE CENTRAL UNIT IS ESTIMATED AND DETERMINED
The largest amount of socket points which are required to be used concurrently at any given point in time determines the capacity of such a central unit, which in turn determines the airflow rate. It does not matter how many socket points a location has—two, one hundred, or even more—the capacity of the central unit is determined solely by this maximum number. For instance, in a given circumstance, if there are 20 socket points and it is only necessary to run four at the same time, the capacity of such a central unit will be only adequate for four points.
There are specific circumstances in which a higher or lower airflow at each point might be required.
The suction pressure that is going to be generated either by the central unit needs to have a decision made about it, and that decision needs to be based on the length and intricacy of the pipeline.
Several Benefits Associated with Utilizing an Industrial Vacuum System
These vacuum systems could be utilized in a variety of work environments; however, what distinguishes this system from others on the market is what sets it apart as the superior option. They make it possible for work to continue without an operator having to wait for another to finish the process of vacuuming or for maintenance employees to undertake the operation. Additionally, the total amount of time spent cleaning and getting rid of waste is cut down significantly by using industrial vacuum cleaners. Both of these factors are advantageous to businesses since they make it possible to cut down on the amount of time and effort spent on tasks that are not directly related to the primary business activity.
The following is a list of some other applications for the industrial vacuum system:
- Clear away any clutter from the loading stations.
- Take off shards of metal and pieces of other materials.
- Clean equipment
Combustible materials can be vacuumed without setting off an explosion if the materials are vacuumed.
Eliminate any spills to reduce the risk of future health and safety problems.
The installation of an industrial central vacuum system pump typically needs the installation of ductwork or vents that suck air through to the dust collector filters and then return it to the building. Vents solely on a single side of the building draw unclean air out while vents on the opposite side of the structure push clean air in. This configuration is referred to as a “push-pull” system.
Another significant component to consider is the nature of the dust that is present in your facility. There are some materials that produce dust that is dangerous or toxic, and this dust needs to be eliminated at the source. This necessitates the utilization of a source capture system, which is a device that collects particulate matter and gasses directly at the point of production.
This simple solution has the potential to significantly increase your cleaning range by granting access to additional locations, both horizontally and vertically. That includes more floors, stairwells, and even adjacent buildings. In addition, it enables your staff to reach all of those tricky catchment places, such as down in pits, beneath conveyors, between machinery, up on ledges, ducts, as well as pipework, etc. Additionally, over one operative can use the system simultaneously in a variety of locations thanks to the system’s scalability.