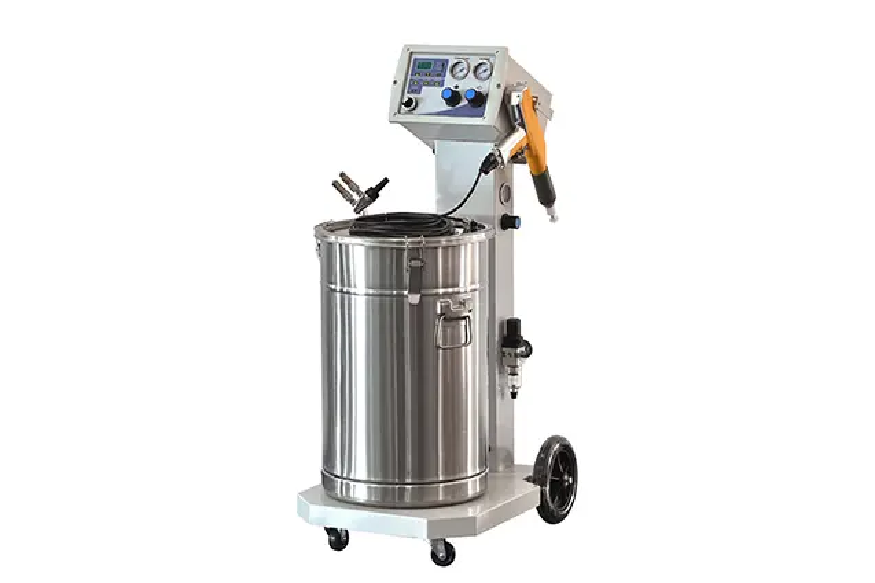
Humidity isn’t something people often think about in a powder coating setup—until it causes trouble. It quietly influences how powder behaves from start to finish. In any shop using a powder coating machine, staying ahead of moisture levels can make or break the end result.
Prevents Powder Clumping Issues
Humidity sneaks in where it’s not wanted—especially around powder storage and delivery. If the air’s too damp, fine powder particles begin sticking together, forming clumps that ruin a smooth spray. This kind of buildup inside hoses or feed lines leads to uneven delivery through the powder coating machine, which can throw off the entire job.
A well-regulated humidity level prevents that clumping from happening. Operators in controlled environments report cleaner feed paths and more consistent material flow. The result is less waste, less downtime, and better performance from the equipment. That consistency keeps the focus on quality, not fixing clogged lines or cleaning out moisture-damaged powder.
Enhances Coating Adhesion Quality
Dry powder needs to land clean and stick right on the first try. If the air is too humid, particles absorb moisture and lose the charge needed to cling properly to the part’s surface. That weak bond leads to poor adhesion—and poor adhesion means coatings can chip, peel, or flake off after curing.
By keeping humidity at a stable, low level, a powder coating machine delivers stronger, more reliable contact between powder and metal. This helps parts pass durability tests and withstand real-world wear without issues. The bond formed in low humidity is not only stronger, it’s also more consistent across batches. That kind of reliability means fewer returns and less rework for production teams.
Maintains Uniform Particle Distribution
Even with the right gear and settings, if the powder behaves differently from pass to pass, the finish will suffer. Moisture in the air causes particles to stick together in midair or travel unevenly through the spray path. This can create patchy zones or uneven layering, no matter how skilled the operator is.
A stable, dry atmosphere keeps particles free-flowing and evenly spaced. That means the powder coating machine can deliver a smooth, continuous spray pattern without having to constantly adjust for changing powder behavior. Uniform distribution leads to clean edges, level finishes, and a lot less rework once the part comes out of the oven.
Reduces Surface Imperfections
Blistering. Pinholes. Craters. These tiny flaws show up like scars on what should be a flawless finish. Moisture trapped between powder and surface during spraying or curing can cause gas to release too late, damaging the coating from the inside out.
Humidity control prevents that damage before it begins. A dry environment ensures the powder goes on clean and cures evenly, leaving no room for steam or vapor to form. The fewer imperfections there are, the smoother the end product—and the more professional it looks in any industry, whether it’s furniture, automotive, or architecture.
Improves Electrostatic Application Consistency
Powder sticks to metal using an electrostatic charge. But damp air can short-circuit that process. Moisture makes it harder for particles to hold a consistent charge, and parts may not retain enough static to attract the powder. That leads to weak coverage, missed corners, or light spots that stand out after curing.
In a dry space, the powder coating machine performs as it’s designed to. Powder picks up the charge cleanly, travels straight to the part, and holds tight until it melts down in the oven. The charge stays stable, allowing even hard-to-reach areas to get covered. That’s not just about looks—it’s about full protection from corrosion or wear.
Minimizes Risk of Coating Contamination
Airborne contamination is already a challenge in any coating process. Add humidity to the mix, and dust or oils have a greater chance of clinging to parts or powder. That results in dirty finishes and costly rework. Contaminants in the powder hopper or on the part can go unnoticed until the oven reveals a ruined coat.
A humidity-controlled workspace lowers the risk by keeping moisture from drawing in pollutants. Dry air doesn’t just protect powder—it protects the whole system. From feed hoppers to the booth to the powder coating machine itself, less moisture means fewer surprises during or after application.
Stabilizes Powder Flow Rates
Powder should flow like fine sand—not like a paste. But moisture turns free-flowing material into sticky clumps, forcing the equipment to work harder and throw off spray rates. If the powder doesn’t flow consistently, the film build will vary across the part, which affects the final texture and coverage.
Dry air helps maintain that ideal powder flow. It keeps material loose and evenly metered, allowing the powder coating machine to operate without sudden changes in pressure or output. This steadiness leads to better predictability and more efficient use of both time and powder. In high-volume production, that kind of flow control adds up fast.