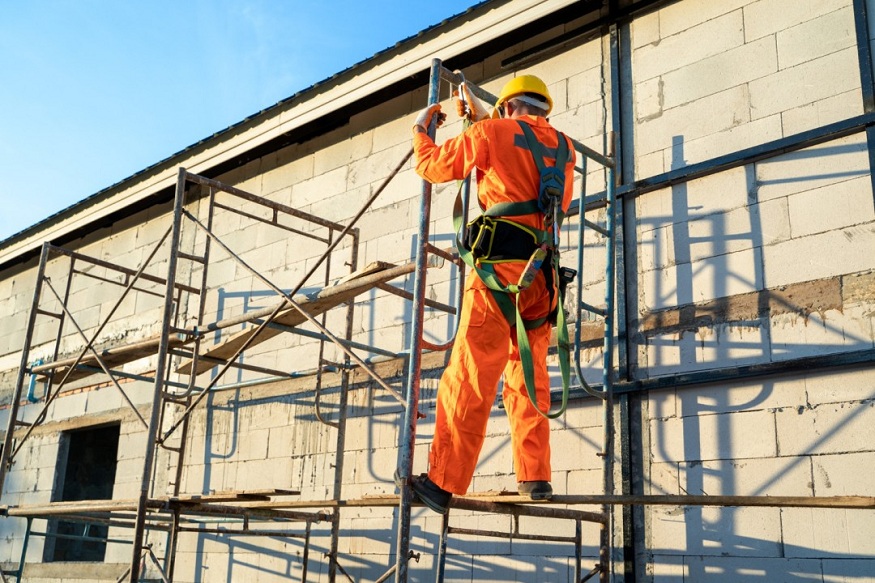
With rising operational costs, it’s essential for industrial manufacturers to focus on reducing expenses, particularly in the area of labor. Since labor costs often account for a large portion of total spending, identifying effective strategies to decrease these costs without undermining safety or productivity is essential. Here are some practical approaches that manufacturers can use to cut labor expenses:
One effective strategy is to enhance facility operations, which can greatly improve productivity. By automating routine tasks, companies reduce reliance on manual labor, increase accuracy, streamline activities, and improve cooperation across various departments.
Investing in cutting-edge technology also helps reduce labor costs. Utilizing modern equipment that is built to manage labor-intensive activities minimizes the need for manual involvement, enhances efficiency, optimizes the use of resources, and maintains consistent quality in production.
Enhancements to scheduling systems also offer significant savings. Using predictive scheduling technologies simplifies the workflow, minimizes idle times, and better distributes tasks, which boosts overall operational performance.
Additionally, optimizing production techniques can substantially lower labor requirements. Collaborating with experts in safe scaffolding engineering, for example, can enhance the efficiency of material handling, improve project execution, and guarantee that tasks are completed safely and effectively with reduced labor needs
Another important factor is employee retention. High turnover rates can inflate costs significantly. Therefore, creating a supportive workplace that values communication, teamwork, and engagement can lead to a more stable and motivated workforce.
By implementing these methods, manufacturers can significantly reduce labor costs while still upholding high standards of safety, productivity, and operational excellence.